Low carbon steel is a cornerstone of the machining and manufacturing industries, valued for its versatility, affordability, and ease of use. This comprehensive guide explores the intricacies of low carbon steel, shedding light on its composition, properties, production, and applications. Whether you’re a professional in the machining industry or simply curious about this widely used material, this article provides an in-depth look at why low carbon steel remains a staple in various sectors.
What Is Low Carbon Steel?
Low carbon steel, often referred to as mild steel,The carbon content in low carbon steel is relatively low, is a type of steel with a carbon content typically ranging from 0.05% to 0.30% by weight. This low carbon concentration distinguishes it from other steel types, such as medium or high carbon steel, and contributes to its unique characteristics. It is one of the most commonly used materials in industries ranging from construction to automotive manufacturing due to its balance of strength, ductility, and cost-effectiveness.
The defining feature of low carbon steel is its relatively low strength compared to high carbon steel, but this is offset by its excellent workability. It can be easily shaped, welded, and machined, making it a favorite among manufacturers. Its affordability also makes it an attractive choice for large-scale projects where cost efficiency is a priority.
Why Is Low Carbon Steel So Popular?
The popularity of low carbon steel stems from its versatility. It is used in everything from household appliances to structural beams in buildings. Its ability to be formed into various shapes without sacrificing structural integrity makes it ideal for applications requiring flexibility and durability. Additionally, its low cost compared to other metals ensures it remains a go-to material for businesses looking to optimize production without compromising quality.
Low Carbon Steel Composition
The composition of low carbon steel is what gives it its distinctive properties. As mentioned, the carbon content in low carbon steel typically ranges from 0.05% to 0.30%. However, carbon is not the only element present. Low carbon steel also contains small amounts of other elements, such as manganese, silicon, and sometimes trace amounts of sulfur and phosphorus.
Key Elements in Low Carbon Steel
- Carbon: The primary element that defines low carbon steel, kept at low levels to enhance ductility and weldability.
- Manganese: Typically present in amounts up to 1.5%, manganese improves the strength and toughness of steel.
- Silicon: Used in small quantities (up to 0.6%), silicon enhances the steel’s strength and elasticity.
- Sulfur and Phosphorus: These are usually kept to a minimum (less than 0.05%) as they can make the steel brittle if present in higher amounts.
Alloying Elements and Their Impact
In some cases, low carbon steel may include additional alloying elements like copper or nickel to enhance specific properties, such as corrosion resistance. These alloyed versions are often used in specialized applications where environmental factors, such as exposure to moisture, are a concern. However, for most general-purpose applications, the standard composition of low carbon steel is sufficient.
Properties of Low Carbon Steel
Low carbon steel is prized for its unique combination of mechanical and physical properties, which make it suitable for a wide range of applications. Below are some of the key properties that define this material.

Mechanical Properties
- Ductility: Low carbon steel is highly ductile, meaning it can be easily drawn into wires or formed into thin sheets without breaking.
- Weldability: Its low carbon content makes it easy to weld without the risk of cracking, a common issue with higher carbon steels.
- Machinability: The material is soft enough to be machined with ease, reducing wear on tools and improving production efficiency.
- Tensile Strength: While not as strong as high carbon steel, low carbon steel has sufficient tensile strength for many structural applications.
Physical Properties
- Density: Low carbon steel has a density of approximately 7.85 g/cm³, similar to other steel types.
- Thermal Conductivity: It conducts heat well, making it suitable for applications requiring heat dissipation.
- Corrosion Resistance: Without additional treatments or alloying, low carbon steel is prone to rust when exposed to moisture, necessitating coatings or galvanization for outdoor use.
- Melting point: It is 1515℃. This value is determined by its chemical composition and metal structure characteristics.
Why These Properties Matter
The combination of these properties makes low carbon steel a versatile material for industries that require materials that are easy to work with yet durable enough for practical use. Its ability to be shaped and welded without compromising structural integrity is particularly valuable in machining and fabrication.
What Are the Types of Low Carbon Steel Grades?
Low carbon steel is available in various grades, each tailored to specific applications based on its composition and processing. The American Iron and Steel Institute (AISI) and the Society of Automotive Engineers (SAE) provide standardized classifications for these grades, typically denoted by a four-digit number.
Common Low Carbon Steel Grades
- AISI 1010: With a carbon content of around 0.10%, this grade is highly formable and used in applications like sheet metal and automotive panels.
- AISI 1020: Containing about 0.20% carbon, this grade offers a good balance of strength and ductility, commonly used in machinery parts.
- A36: A popular structural steel grade with excellent weldability, often used in construction for beams and plates.
- C1008/C1010: These grades are often used in cold-rolled or hot-rolled forms for applications requiring smooth surfaces and high formability.
How Grades Affect Performance
The choice of grade depends on the specific requirements of the project. For example, AISI 1010 is ideal for applications requiring deep drawing, while A36 is better suited for structural components due to its higher strength. Understanding the differences between these grades allows manufacturers to select the most appropriate material for their needs.
How Is Low Carbon Steel Made?
The production of low carbon steel involves several stages, from raw material extraction to final processing. The process begins with the extraction of iron ore, which is then refined and combined with other elements to create steel with the desired properties.
The Steel-Making Process
- Iron Ore Extraction: Iron ore is mined and processed to remove impurities, resulting in pig iron.
- Blast Furnace: Pig iron is melted in a blast furnace, where it is combined with carbon and other elements.
- Basic Oxygen Furnace (BOF): The molten iron is refined in a BOF, where oxygen is blown through the material to reduce the carbon content to the desired level (0.05%–0.30% for low carbon steel).
- Casting: The molten steel is cast into slabs, billets, or blooms, which are then shaped into final products through rolling or forging.
- Heat Treatment: Some low carbon steel undergoes heat treatment, such as annealing, to enhance its ductility and reduce internal stresses.
Modern Advancements in Production
Modern steel-making techniques, such as electric arc furnaces (EAF), have made the production of low carbon steel more efficient and environmentally friendly. EAFs use recycled scrap metal, reducing the need for raw materials and lowering energy consumption. These advancements align with the industry’s push toward sustainability.
What Are the Uses of Low Carbon Steel?
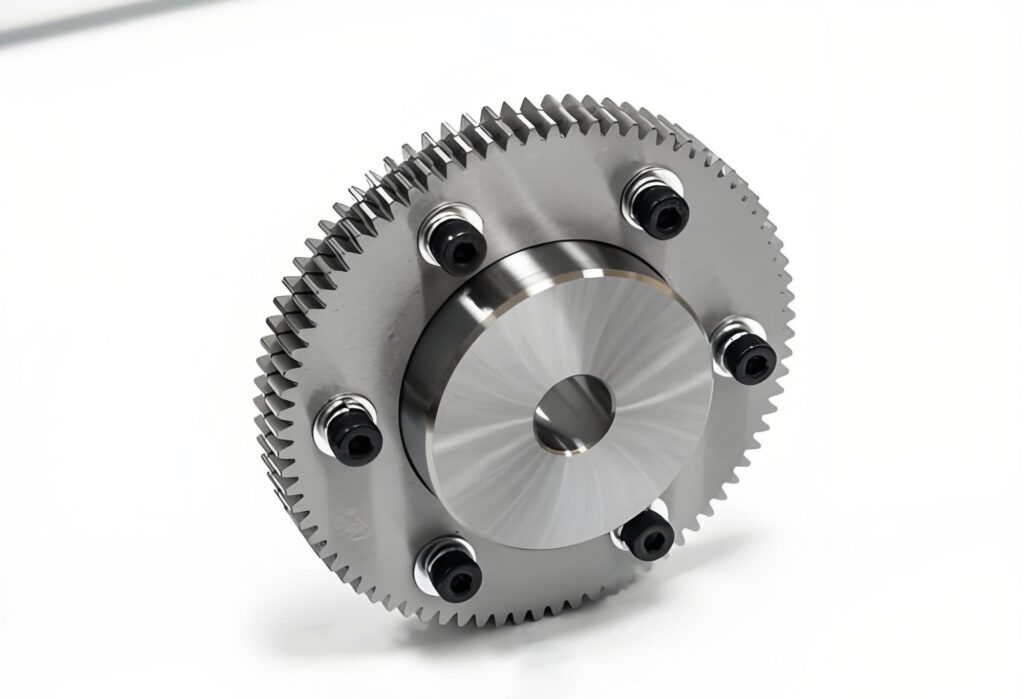
Low carbon steel’s versatility makes it a critical material in numerous industries. Its ability to be formed, welded, and machined with ease ensures its widespread use in both industrial and consumer applications.
Industrial Applications
- Construction: Low carbon steel is used in structural components like beams, columns, and rebar due to its strength and affordability.
- Automotive: Car bodies, chassis, and panels are often made from low carbon steel because of its formability and lightweight properties.
- Machinery: Gears, shafts, and other machine components benefit from the material’s machinability and durability.
- Pipelines: Low carbon steel is used in pipelines for oil, gas, and water transport, often with protective coatings to prevent corrosion.
Consumer Products
- Appliances: Refrigerators, washing machines, and ovens often use low carbon steel for their frames and panels.
- Furniture: Metal furniture, such as desks and chairs, frequently incorporates low carbon steel for its durability and aesthetic appeal.
- Cookware: Some cookware, like frying pans, uses low carbon steel for its heat conductivity and affordability.
Emerging Applications
With advancements in material science, low carbon steel is finding new applications in renewable energy sectors, such as wind turbine towers and solar panel frames. Its affordability and recyclability make it an attractive choice for sustainable projects.
The Advantages and Disadvantages of Low Carbon Steel
Like any material, low carbon steel has its strengths and weaknesses. Understanding these can help manufacturers make informed decisions about when to use it.
Advantages
- Cost-Effective: Low carbon steel is one of the most affordable metals, making it ideal for large-scale projects.
- Ease of Fabrication: Its ductility and weldability make it easy to shape and join, reducing production costs.
- Recyclability: Low carbon steel is 100% recyclable, supporting sustainable manufacturing practices.
- Versatility: Its wide range of applications makes it suitable for diverse industries, from construction to consumer goods.
Disadvantages
- Lower Strength: Compared to high carbon or alloy steels, low carbon steel has lower tensile strength, limiting its use in high-stress applications.
- Corrosion Susceptibility: Without protective coatings, low carbon steel is prone to rust, especially in humid or marine environments.
- Limited Hardness: Its low carbon content makes it less suitable for applications requiring high wear resistance, such as cutting tools.
Balancing the Pros and Cons
For many applications, the advantages of low carbon steel outweigh its limitations. By applying coatings like galvanization or using alloying elements, manufacturers can mitigate its weaknesses, such as corrosion susceptibility, while capitalizing on its affordability and workability.
Low Carbon Steel vs High Carbon Steel
When choosing between low carbon steel and high carbon steel, understanding their differences is crucial. High carbon steel typically contains 0.6% to 1.0% carbon, making it significantly stronger but less ductile than its low carbon counterpart.
Key Differences
- Strength: High carbon steel is much stronger and harder, making it suitable for tools and blades, while low carbon steel is better for structural components.
- Ductility: Low carbon steel is more ductile, allowing it to be formed into complex shapes without breaking.
- Weldability: Low carbon steel is easier to weld due to its lower carbon content, while high carbon steel requires special techniques to avoid cracking.
- Cost: Low carbon steel is generally cheaper, making it more cost-effective for large-scale projects.
Choosing the Right Material
The choice between low carbon and high carbon steel depends on the application. For projects requiring strength and hardness, such as cutting tools, high carbon steel is the better choice. However, for applications prioritizing formability and cost, low carbon steel is often the preferred option.
Practical Examples
- Low Carbon Steel: Used in car bodies, pipelines, and structural beams.
- High Carbon Steel: Used in knives, drill bits, and springs.
By understanding the trade-offs between these materials, manufacturers can select the steel type that best aligns with their project requirements.
The Role of Low Carbon Steel in Modern Manufacturing
Low carbon steel continues to be a vital material in the machining and manufacturing industries. Its affordability, versatility, and ease of use make it an essential component in everything from skyscrapers to household appliances. As industries increasingly focus on sustainability, the recyclability of low carbon steel positions it as a key player in environmentally conscious manufacturing.
Precionn’s Commitment to Quality
At Precionn, a leader in the machining industry, low carbon steel is a cornerstone of many of our projects. With a commitment to precision and innovation, Precionn leverages the unique properties of low carbon steel to deliver high-quality components for a wide range of applications. Our expertise in machining ensures that every product meets the highest standards of durability and performance. To learn more about how Precionn can support your manufacturing needs, visit our website at Precionn’s site.