Carbon steel play a crucial role in the production of high-quality components. At Precionn, leveraging our expertise in processing and our unwavering pursuit of excellence, we utilize carbon steel to manufacture durable and precise components suitable for various industries. This blog will delve into this alloy, covering aspects such as its composition, characteristics, types, applications, advantages, and disadvantages, providing valuable insights for engineers and manufacturers.
What is Carbon Steel?
Carbon steel is a fundamental material in manufacturing, valued for its strength, versatility, and cost-effectiveness. It is an alloy primarily composed of iron and carbon, with carbon content typically ranging from 0.05% to 2.0%. Unlike stainless steel, which includes chromium for corrosion resistance, carbon steel’s properties are largely determined by its carbon content, making it a go-to choice for applications requiring durability and adaptability.
This material is widely used in industries such as construction, automotive, and aerospace due to its ability to be tailored for specific purposes. Whether it’s for structural beams or precision tools, carbon steel’s simplicity and performance make it indispensable. Precionn leverages its machining expertise to transformthis alloy into components that meet exacting standards, ensuring reliability and precision in every project.
Composition of Carbon Steel
The composition of this alloy is relatively straightforward, consisting mainly of iron and carbon, with trace amounts of other elements to enhance specific properties. The carbon content is the primary factor influencing the material’s mechanical characteristics, such as strength and hardness. Other elements, like manganese and silicon, are often included to improve performance.
- Iron: The base element, forming the majority of the alloy.
- Carbon: Ranging from 0.05% to 2.0%, carbon determines the steel’s strength and hardness.
- Manganese: Typically present up to 1.65%, it enhances strength and toughness.
- Silicon: Added in small amounts (up to 0.6%) to improve strength and elasticity.
- Sulfur and Phosphorus: Found in trace amounts, these elements can influence machinability and brittleness.
Properties of Carbon Steel
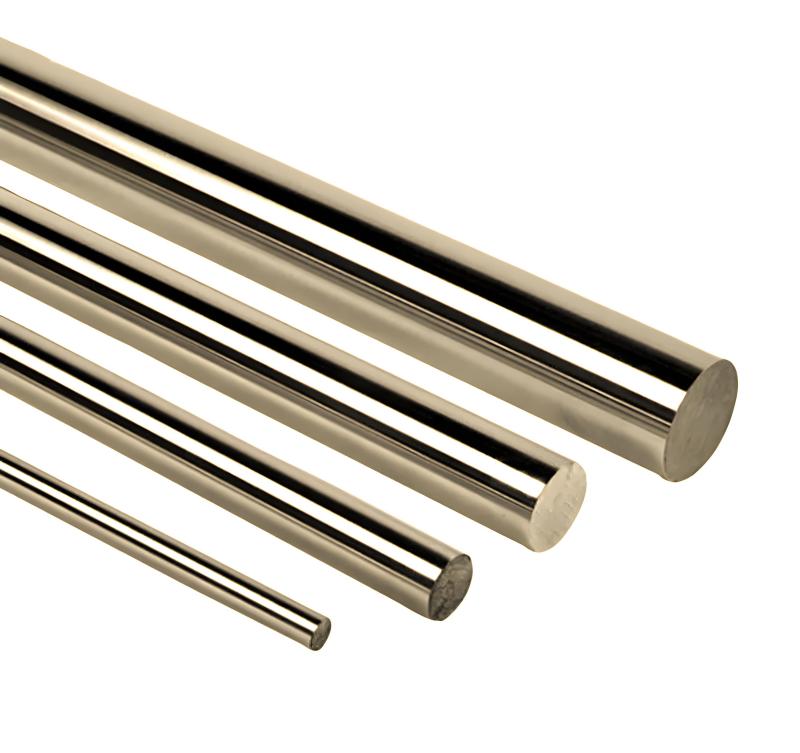
Carbon steel’s properties make it a versatile material for a wide range of applications. Its mechanical characteristics, including strength, hardness, and ductility, vary based on carbon content and processing methods. These properties discussed below are relevant to industrial applications.
Carbon Steel Density
The density of this alloy typically falls between 7.75 and 7.85 g/cm³, depending on its composition and alloying elements. This density is slightly lower than that of pure iron due to the presence of carbon and other elements. The material’s density contributes to its strength and durability.
In machining, understanding this alloy density is essential for calculating weight, determining load-bearing capacity, and designing components with optimal strength-to-weight ratios. For instance, Precionn uses this knowledge to create parts that balance durability and efficiency, catering to industries like automotive and construction where weight considerations are critical.
Carbon Steel Hardness
Hardness is one of the most defining properties of carbon steel, directly influenced by its carbon content and heat treatment processes. Measured using scales like Rockwell (HRC) or Brinell (HB), this alloyhardness varies significantly across its grades:
- Low-Carbon Steel (0.05% to 0.25% carbon): This grade is relatively soft, with Rockwell hardness values typically ranging from 50 to 70 HRB. Its lower hardness makes it highly ductile and easy to machine, ideal for forming processes like bending and stamping.
- Medium-Carbon Steel (0.25% to 0.60% carbon): Offering a balance of hardness and flexibility, this grade typically achieves hardness values of 20 to 30 HRC after heat treatment. It’s suitable for components like gears and axles that require moderate strength and wear resistance.
- High-Carbon Steel (0.60% to 2.0% carbon): Known for its exceptional hardness (up to 60 HRC or higher with heat treatment), high-carbon steel is used for cutting tools, knives, and springs. However, its increased hardness comes at the cost of brittleness, requiring careful handling during machining.
Heat treatment processes, such as quenching (rapid cooling) and tempering (controlled reheating), significantly enhance this alloy hardness. For example, quenching can increase the hardness of high-carbon steel by forming a martensitic structure, while tempering reduces brittleness to achieve a balanced toughness. Precionn’s expertise in machining allows us to work with carbon steel across this hardness spectrum, ensuring that components meet precise performance requirements, whether for durable machinery parts or sharp cutting tools.
Tensile Strength and Yield Strength
Tensile strength, the ability of this alloy to withstand pulling forces, is another critical property that varies with carbon content. Low-carbon steel typically has a tensile strength of 400–550 MPa, making it suitable for applications where flexibility is more important than extreme strength. Medium-carbon steel, with tensile strengths of 600–800 MPa, is ideal for components requiring a balance of strength and ductility, such as automotive crankshafts. High-carbon steel can achieve tensile strengths exceeding 1000 MPa, but its brittleness limits its use to specialized applications.
Yield strength, the point at which carbon steel begins to deform permanently, follows a similar trend. Low-carbon steel has a lower yield strength (around 250–350 MPa), while high-carbon steel can exceed 700 MPa after heat treatment. These properties make this alloy a versatile choice for structural and mechanical applications, where the balance of strength and formability is critical. Precionn leverages these properties to design components that withstand specific stresses while maintaining dimensional accuracy.
Ductility and Formability
Ductility, the ability of carbon steel to deform without breaking, is highest in low-carbon steel due to its lower carbon content. This makes it ideal for processes like rolling, drawing, and forging, where the material is shaped into sheets, wires, or complex forms. For example, low-carbon steel is commonly used to produce sheet metal for car bodies or structural components like I-beams. As carbon content increases, ductility decreases, with high-carbon steel being less formable but more resistant to wear.
Formability is closely tied to ductility and is a key consideration in machining. Low and medium-carbon steels are easier to machine and form, allowing for intricate designs and tight tolerances.
Thermal Conductivity
Carbon steel’s thermal conductivity, typically ranging from 40 to 50 W/m·K, is lower than that of pure iron or copper but sufficient for many applications. This property determines how effectively the material conducts heat, which is crucial in environments involving high temperatures, such as engine components or industrial machinery. While this alloy is not as thermally conductive as some specialized alloys, its ability to withstand moderate heat makes it suitable for pipelines, pressure vessels, and heat exchangers.
In machining, thermal conductivity affects tool wear and cutting efficiency. High-carbon steel, with its greater hardness, generates more heat during machining, requiring specialized tools and cooling techniques.
Corrosion Behavior
Unlike stainless steel, this alloy is susceptible to corrosion, particularly in moist or chemically aggressive environments. This is due to the absence of chromium, which forms a protective oxide layer in stainless steel. The corrosion behavior of carbon steel depends on its environment and can be mitigated through coatings, such as galvanization or paint, or through regular maintenance.
For example, this alloy used in pipelines is often coated with zinc to prevent rust, while structural components may be painted or treated with anti-corrosion agents. In machining, corrosion resistance is less critical during production, but Precionn ensures that finished components are treated appropriately to meet environmental demands, extending their service life in applications like construction and energy.
Wear Resistance and Fatigue Strength
Wear resistance, the ability to withstand surface abrasion, is higher in high-carbon steel due to its hardness. This makes it ideal for applications like cutting tools and wear plates, where prolonged contact with abrasive surfaces is common. Medium-carbon steel offers moderate wear resistance, suitable for gears and bearings, while low-carbon steel is less resistant but more cost-effective for non-abrasive environments.
Fatigue strength, the ability to withstand repeated loading without failure, is another important property. Medium and high-carbon steels, especially when heat-treated, exhibit good fatigue strength, making them suitable for dynamic applications like springs and axles.
Magnetic Properties
This alloy, particularly low and medium-carbon grades, is ferromagnetic, meaning it can be magnetized and is attracted to magnets. This property is useful in applications like electric motors, transformers, and magnetic clamps. High-carbon steel may exhibit slightly reduced magnetism due to its microstructure, but it remains magnetic in most cases. This property is often considered in machining and assembly processes, where magnetic properties can aid in material handling or component alignment.
Different Types of Carbon Steel Grades
This alloyl is classified into three main grades based on its carbon content: low, medium, and high. Each grade has distinct characteristics that make it suitable for specific applications, allowing manufacturers to select the best type for their needs.
Low Carbon Steel
Low-carbon steel, also known as mild steel, contains 0.05% to 0.25% carbon. It is highly ductile and easy to form, making it ideal for applications requiring flexibility, such as sheet metal, wire, and structural components. While it has lower strength compared to other grades, its affordability and workability make it a popular choice for construction, automotive parts, and general manufacturing.
Medium Carbon Steel
With a carbon content of 0.25% to 0.60%, medium-carbon steel offers a balance of strength, hardness, and ductility. It is commonly used in applications requiring moderate hardness, such as gears, axles, and machinery components. Heat treatment can enhance its properties, making it suitable for industries like aerospace and automotive, where durability and flexibility are essential.
High Carbon Steel
High-carbon steel, containing 0.60% to 2.0% carbon, is known for its exceptional hardness and strength. However, it is less ductile and more prone to brittleness, making it ideal for specialized applications like cutting tools, knives, and springs. Its ability to maintain a sharp edge makes it a favorite in precision machining.
Applications of carbon steel material

Carbon steel’s versatility makes it a cornerstone in numerous industries. Its strength, affordability, and adaptability allow it to be used in a wide range of applications, from large-scale infrastructure to precision components.
- Construction: Low-carbon steel is widely used for structural beams, columns, and rebar due to its strength and cost-effectiveness. It forms the backbone of buildings, bridges, and highways.
- Automotive: Medium-carbon steel is used for axles, crankshafts, and other components requiring a balance of strength and flexibility.
- Tool Manufacturing: High-carbon steel is the material of choice for cutting tools, drill bits, and knives due to its hardness and ability to maintain a sharp edge.
- Pipelines and Energy: This alloy is used in pipelines and pressure vessels for its durability and ability to withstand high-pressure environments.
- Machinery: From gears to fasteners, carbon steel is a key material in manufacturing equipment and machinery components.
Precionn specializes in machining this alloy to create precision parts for these and other applications. Our state-of-the-art CNC machining capabilities ensure that every component meets the highest standards of quality and performance, delivering reliable solutions for our clients.
Advantages and Disadvantages of Carbon Steel
Like any material, this alloy has its strengths and limitations. Understanding these trade-offs is crucial for selecting the right material for a given application.
Advantages
- Affordability: This alloy is more cost-effective than stainless steel or other alloys, making it a budget-friendly option for large-scale projects.
- Strength and Durability: Depending on the carbon content, This alloy offers excellent strength, making it suitable for structural and high-stress applications.
- Versatility: With various grades and heat treatment options, This alloy can be tailored to meet a wide range of requirements.
- Machinability: Low and medium-carbon steels are relatively easy to machine, allowing for precision manufacturing of complex components.
Disadvantages
- Corrosion Susceptibility: Unlike stainless steel, This alloy is prone to rust and corrosion, requiring coatings or regular maintenance in certain environments.
- Brittleness in High-Carbon Steel: While high-carbon steel is extremely hard, it can be brittle, limiting its use in applications requiring flexibility.
- Limited Heat Resistance: This alloy may not perform well in extremely high-temperature environments compared to specialized alloys.
By understanding these advantages and disadvantages, manufacturers can apply protective measures, such as coatings or galvanization, to mitigate limitations.
Choosing the Right Carbon Steel for Your Project
Selecting the appropriate carbon steel grade depends on various factors, including mechanical demands, environmental exposure, fabrication requirements, and cost constraints. Here are a few considerations:
- Strength vs. Ductility: High-carbon steel provides increased hardness but at the cost of ductility. For structural components requiring flexibility, low or medium-carbon steel may be better.
- Machinability: Low-carbon grades are easier to cut and weld, making them suitable for complex shapes or large-scale production.
- Wear Resistance: High-carbon or ultra-high-carbon steel is better for applications involving friction or heavy usage.
- Budget: Lower carbon steels are more affordable and suitable for general-purpose applications.
Precionn assists clients in choosing the right this alloy grade by considering all technical and economic aspects of their project, ensuring optimized performance and cost-efficiency.
Conclusion
Carbon steel remains a cornerstone of modern manufacturing, offering a unique combination of strength, versatility, and affordability. From construction to precision machining, this material plays a critical role in countless applications. At Precionn, we harness the power of carbon steel to deliver high-quality, precision-machined components that meet the needs of industries worldwide. Our expertise in material selection, machining, and quality control ensures that every project is completed to the highest standards.
For more information about how Precionn can support your carbon steel machining needs, visit our website or contact our team today. Let us help you bring your projects to life with precision, durability, and expertise.