Stainless steel is a versatile and widely used material in industries ranging from construction to kitchenware, but one question often pops up: Is stainless steel magnetic? For those new to the world of metals, this topic can seem confusing. The short answer is that some stainless steels are magnetic, while others are not. This blog dives deep into the science, types, and practical implications of magnetism in stainless steel, breaking it down in a way that’s easy to understand for everyone. Whether you’re a hobbyist, a professional, or just curious, this guide will clarify everything you need to know about stainless steel and magnetism.
Is Stainless Steel Magnetic?
The question “Is stainless steel magnetic?” is a common one, and the answer depends on the specific type of stainless steel. Stainless steel is an alloy primarily made of iron, chromium, and sometimes nickel, carbon, or other elements. Its magnetic properties hinge on its internal structure, which varies across different types. Broadly speaking, stainless steel falls into two categories when it comes to magnetism: magnetic and non-magnetic.
Magnetic stainless steels, like ferritic and martensitic grades, are attracted to magnets due to their iron-heavy crystal structures. On the other hand, austenitic stainless steels, which often contain nickel, are typically non-magnetic because of their different atomic arrangement. However, even this isn’t a hard-and-fast rule, as factors like cold working or heat treatment can alter magnetism in some cases. Let’s explore why this happens and what it means.
What Is Magnetic Stainless Steel?
Magnetic stainless steel refers to stainless steel alloys that exhibit magnetic properties, meaning they can be attracted to a magnet or even act as magnets themselves. This magnetism comes from the arrangement of atoms in the steel’s crystal structure. To understand this, think of stainless steel as a recipe: the ingredients (elements like iron, chromium, or nickel) and how they’re mixed (the crystal structure) determine whether the final product sticks to a magnet.
Ferritic and martensitic stainless steels are the most common magnetic types. Ferritic stainless steels, like grades 430 or 409, contain a high amount of iron and a body-centered cubic (BCC) crystal structure, which makes them magnetic. Martensitic stainless steels, such as grades 410 or 420, also have a similar structure and are magnetic due to their iron content and heat treatment processes. Austenitic stainless steels, like 304 or 316, are usually non-magnetic but can become slightly magnetic under certain conditions, which we’ll discuss later.
What Makes Stainless Steel Magnetic?
The magnetism of stainless steel comes down to its microstructure and composition. Here’s a simple breakdown of what makes some stainless steels magnetic:
The Role of Crystal Structure
The key to magnetism lies in the crystal structure of the steel. Stainless steels with a ferritic or martensitic structure have a body-centered cubic (BCC) arrangement, which allows the iron atoms to align in a way that supports magnetism. In contrast, austenitic stainless steels have a face-centered cubic (FCC) structure, which disrupts the alignment needed for magnetism, making them non-magnetic in most cases.
The Influence of Alloying Elements
The elements in stainless steel also play a big role. Iron is naturally magnetic, so stainless steels with high iron content, like ferritic grades, are more likely to be magnetic. Chromium, a key component in all stainless steels, doesn’t significantly reduce magnetism. However, adding nickel, as in austenitic grades like 304 or 316, stabilizes the FCC structure, reducing or eliminating magnetism. Other elements, like carbon or molybdenum, can also influence the structure and magnetic behavior.
Processing and Magnetism
Manufacturing processes like cold working (e.g., bending or rolling) or heat treatment can change a stainless steel’s magnetic properties. For example, cold working an austenitic stainless steel can transform some of its structure into martensite, a magnetic phase, making it slightly magnetic. This is why a non-magnetic grade like 304 might show weak magnetism after being heavily processed.
Which Types of Stainless Steel Are Magnetic?
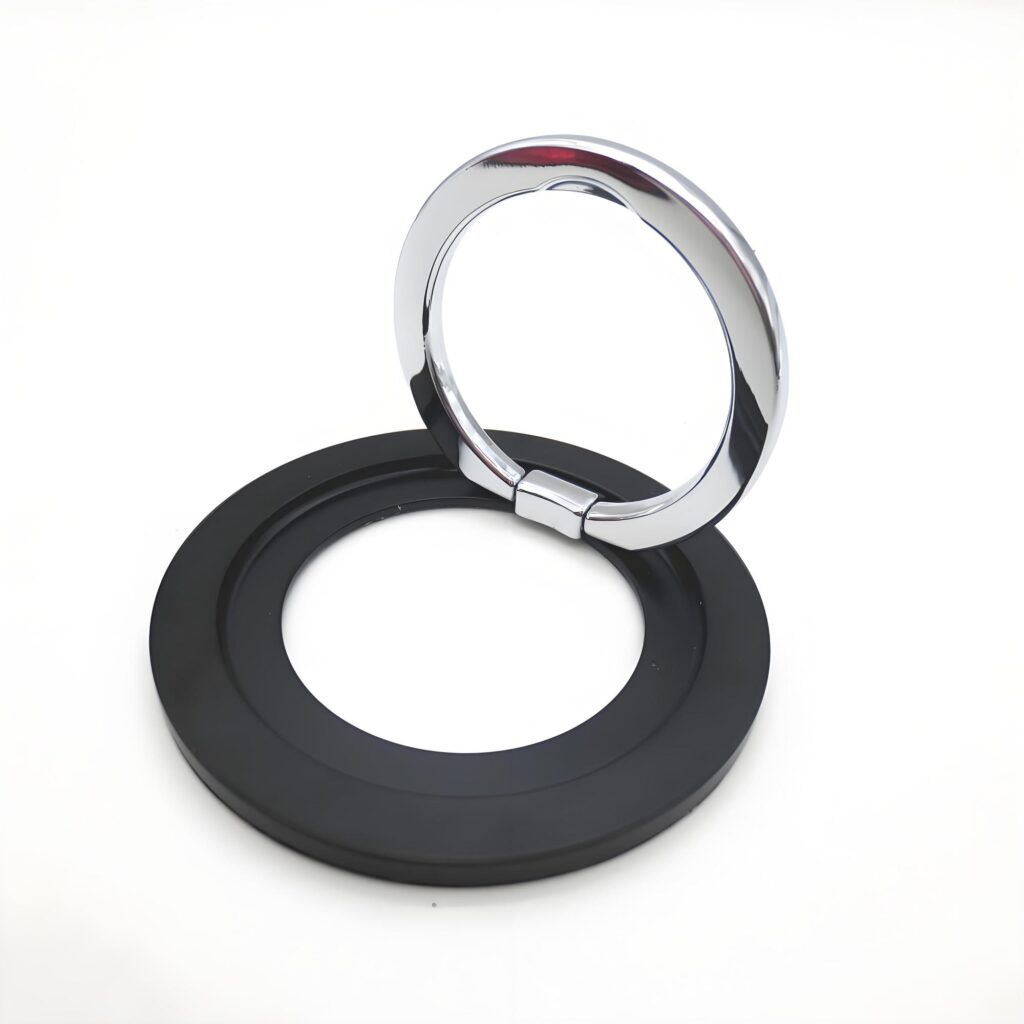
Not all stainless steels are created equal when it comes to magnetism. Here’s a closer look at the main types and their magnetic properties:
Ferritic Stainless Steels
Ferritic stainless steels, such as grades 430, 409, and 439, are magnetic. These alloys contain 10-27% chromium and low amounts of carbon, with little to no nickel. Their BCC structure makes them strongly magnetic, and they’re often used in applications like automotive exhaust systems, kitchen appliances, and decorative trims.
Martensitic Stainless Steels
Martensitic stainless steels, like grades 410, 420, and 440, are also magnetic. These alloys have higher carbon content than ferritic grades and undergo heat treatment to achieve a hard, strong structure. Their magnetic properties make them suitable for cutlery, surgical tools, and industrial equipment where strength and magnetism are beneficial.
Austenitic Stainless Steels
Austenitic stainless steels, such as grades 304, 316, and 321, are typically non-magnetic due to their FCC structure, which is stabilized by nickel and other elements. These grades are widely used in food processing, chemical industries, and medical equipment because of their corrosion resistance and non-magnetic nature. However, as mentioned earlier, cold working can induce slight magnetism in these grades.
Duplex and Precipitation-Hardening Stainless Steels
Duplex stainless steels, which combine austenitic and ferritic structures, are partially magnetic because of their ferritic component. Grades like 2205 are used in harsh environments like oil and gas industries. Precipitation-hardening stainless steels, like 17-4 PH, can also be magnetic, depending on their heat treatment and composition.
Why Is Magnetism Important in Stainless Steel?
Magnetism in stainless steel matters for both practical and technical reasons. Understanding whether a stainless steel is magnetic can help in material selection, quality control, and even troubleshooting in manufacturing. Here’s why magnetism is significant:
Material Selection for Applications
In industries like electronics or medical equipment, non-magnetic materials are often preferred to avoid interference with sensitive devices. For example, austenitic stainless steels like 316 are chosen for MRI machines because they won’t be affected by strong magnetic fields. On the other hand, magnetic stainless steels like 430 are ideal for applications like magnetic knife strips or automotive parts where magnetism is harmless or even useful.
Quality Control and Identification
Magnetism can serve as a quick way to identify or verify stainless steel grades during manufacturing or inspection. A simple magnet test can help distinguish between austenitic and ferritic/martensitic grades, ensuring the right material is used for the job. This is especially useful in machining shops where different grades might look similar but have different properties.
Performance in Harsh Environments
Magnetic stainless steels often have different mechanical properties, like higher strength or hardness, compared to non-magnetic ones. For instance, martensitic grades are magnetic and exceptionally strong, making them suitable for tools and blades. Understanding magnetism helps engineers choose the right stainless steel for specific conditions, balancing factors like corrosion resistance, strength, and cost.
How Do You Tell If Stainless Steel Is Magnetic?
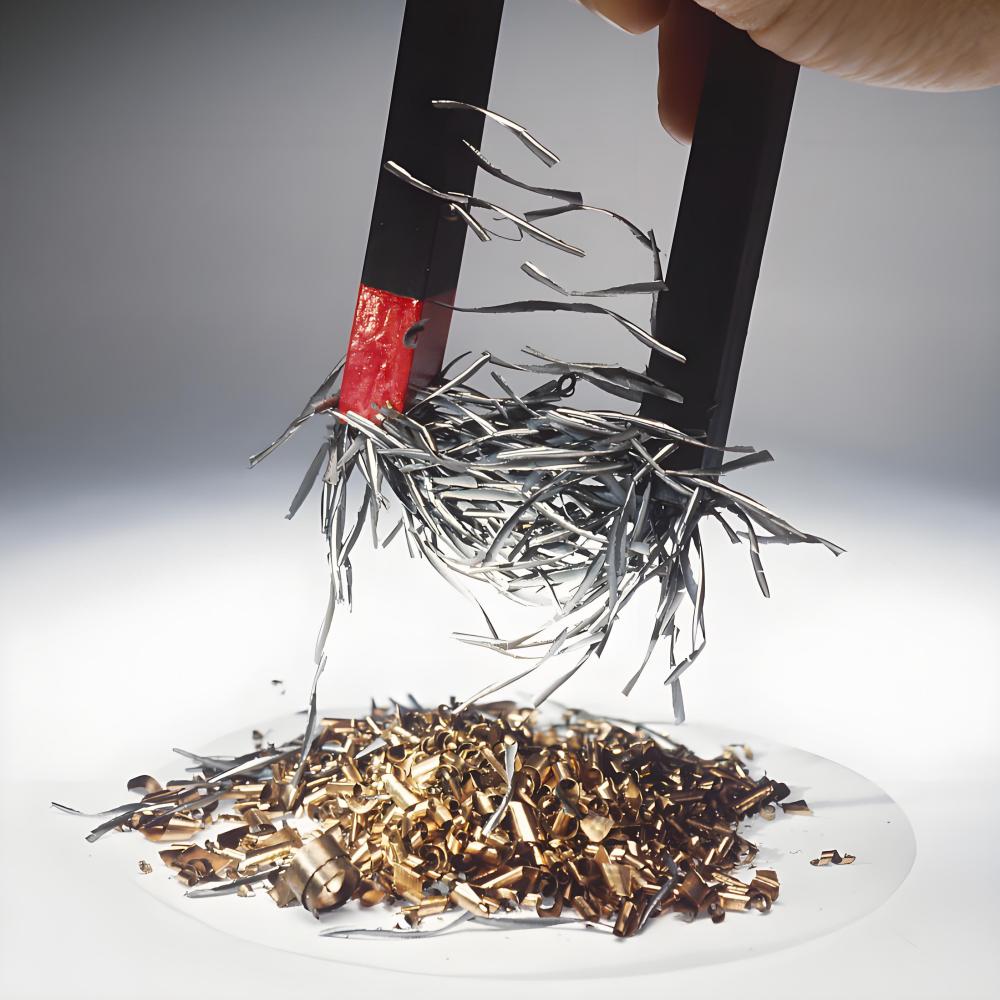
Determining whether a piece of stainless steel is magnetic is straightforward and doesn’t require fancy equipment. Here are some practical ways to test magnetism:
The Magnet Test
The simplest method is to use a magnet. Hold a standard magnet (like a refrigerator magnet) close to the stainless steel. If the material is attracted to the magnet, it’s likely ferritic or martensitic. If there’s no attraction, it’s probably austenitic, though slight magnetism could indicate cold-worked austenitic steel.
Visual and Contextual Clues
While not foolproof, the appearance and application of stainless steel can offer hints. For example, ferritic stainless steels are often used in decorative or automotive applications, while austenitic grades are common in food-grade or chemical equipment. Checking the grade (e.g., 304, 430) stamped on the material can also confirm its magnetic properties.
Professional Testing
For precise identification, professionals might use tools like X-ray fluorescence (XRF) analyzers to determine the alloy’s composition or conduct metallographic analysis to examine its microstructure. These methods are more common in industrial settings, like machining shops, where accuracy is critical.
Things to Keep in Mind
Keep in mind that the magnet test isn’t always definitive. Cold-worked austenitic stainless steel might show weak magnetism, and some magnetic grades might have weaker attraction depending on their composition. If magnetism is critical for your application, consult with a material expert or refer to the alloy’s technical data sheet.
Other Factors That Affect Magnetism
Beyond the type of stainless steel, several other factors can influence its magnetic behavior:
Cold Working
As mentioned earlier, cold working (e.g., bending, rolling, or stamping) can induce magnetism in austenitic stainless steels by transforming some of the austenite into martensite. The degree of magnetism depends on how much the material was worked and its original composition.
Heat Treatment
Heat treatment processes, like annealing or quenching, can alter the microstructure of stainless steel. For example, annealing an austenitic stainless steel can reduce any magnetism caused by cold working, while specific heat treatments can enhance magnetism in martensitic grades.
Environmental Conditions
In rare cases, extreme environmental conditions, like very low temperatures, can affect magnetism. For instance, some austenitic stainless steels may become slightly magnetic at cryogenic temperatures due to phase transformations.
Practical Applications of Magnetic and Non-Magnetic Stainless Steel
Understanding magnetism helps in choosing the right stainless steel for specific applications. Here are a few examples:
- Magnetic Stainless Steels: Ferritic grades like 430 are used in household appliances (e.g., refrigerators, dishwashers) and automotive trim because of their cost-effectiveness and magnetic properties. Martensitic grades like 420 are ideal for cutlery and tools due to their hardness and magnetism.
- Non-Magnetic Stainless Steels: Austenitic grades like 304 and 316 are popular in food processing, medical devices, and chemical plants because of their corrosion resistance and non-magnetic nature, which prevents interference with sensitive equipment.
- Mixed Applications: Duplex stainless steels, with their partial magnetism, are used in industries like oil and gas, where both strength and corrosion resistance are critical.
Choosing the Right Stainless Steel for Your Needs
When selecting stainless steel, consider the following:
- Magnetism Requirements: Does your application require a non-magnetic material (e.g., for electronics) or is magnetism acceptable?
- Corrosion Resistance: Austenitic grades generally offer better corrosion resistance, while ferritic and martensitic grades may need coatings in harsh environments.
- Strength and Durability: Martensitic grades are stronger but less corrosion-resistant, while austenitic grades are more ductile.
- Cost: Ferritic grades are often more affordable than austenitic or duplex grades.
Consulting with a machining expert or supplier can help you pick the right grade for your project, ensuring the best balance of properties.
Conclusion: Trust Precionn for Your Stainless Steel Needs
Magnetism in stainless steel is a fascinating topic that reveals the complexity and versatility of this material. Whether you’re working with magnetic ferritic or martensitic grades or non-magnetic austenitic ones, understanding these properties can help you make informed decisions for your projects. From kitchen appliances to industrial machinery, the right stainless steel can make all the difference.
At Precionn, we specialize in precision machining and have deep expertise in working with all types of stainless steel. Whether you need help selecting the right grade, machining complex parts, or understanding material properties like magnetism, our team is here to support you. Visit our website to learn more about our services and how we can bring precision to your projects. With Precionn, you’re not just getting parts—you’re getting quality, expertise, and reliability.