Martensitic stainless steel is a fascinating material that plays a crucial role in various industries, from cutlery to aerospace. Known for its strength and durability, this type of stainless steel is a go-to choice for applications requiring toughness and corrosion resistance. This blog explores what martensitic stainless steel is, how it’s made, its properties, types, applications, benefits, and limitations, all in a way that’s easy to understand, even for those new to the world of machining and materials.
What Is Martensitic Stainless Steel?
This aolly is a type of stainless steel characterized by its high strength and hardness. Unlike other stainless steels, such as austenitic or ferritic, martensitic stainless steel can be heat-treated to achieve exceptional mechanical properties. Its name comes from its microstructure, called martensite, which forms during a specific cooling process. This microstructure gives the material its unique combination of strength, hardness, and moderate corrosion resistance.
Think of martensitic stainless steel as the “tough guy” of the stainless steel family. It’s not as corrosion-resistant as its cousin, austenitic stainless steel, but it makes up for it with superior strength and wear resistance. This makes it ideal for applications where durability is key, such as in tools, blades, and mechanical components.
What Is Martensitic Stainless Steel Made Of?
Martensitic stainless steel is an alloy primarily composed of iron, chromium, and carbon, with other elements added to enhance specific properties. Here’s a breakdown of its key components:
- Iron: The base metal, providing the structural foundation.
- Chromium (10-18%): Gives stainless steel its corrosion resistance by forming a protective oxide layer on the surface.
- Carbon (0.1-1.2%): Increases hardness and strength, especially after heat treatment.
- Other Elements: Small amounts of nickel, molybdenum, or manganese may be added to improve toughness, corrosion resistance, or other characteristics.
The exact composition depends on the specific grade of martensitic stainless steel. For example, higher carbon content increases hardness but may reduce corrosion resistance, while additional chromium enhances protection against rust.
The production process involves melting these elements together in precise proportions, followed by casting and forming. The real magic happens during heat treatment, where the steel is heated to high temperatures and then rapidly cooled (quenched) to form the martensitic structure. Tempering, a secondary heat treatment, may follow to reduce brittleness while maintaining hardness.
What Are the Properties of Martensitic Stainless Steel?
Martensitic stainless steels stands out due to its unique combination of properties, which make it suitable for demanding applications. Here are its key characteristics:
- High Strength and Hardness: Thanks to its martensitic structure, this steel can be hardened through heat treatment, making it much stronger than ferritic or austenitic stainless steels.
- Moderate Corrosion Resistance: While not as corrosion-resistant as austenitic grades, it offers decent protection against rust, especially in mild environments.
- Magnetic: Unlike austenitic stainless steel, martensitic grades are magnetic, which can be useful in certain applications.
- Wear Resistance: Its hardness makes it resistant to wear and abrasion, ideal for cutting tools and mechanical parts.
- Brittleness: High carbon content can make some grades brittle, especially if not properly tempered.
- Machinability: Depending on the grade, martensitic stainless steel can be challenging to machine due to its hardness, requiring specialized tools and techniques.
These properties make martensitic stainless steel a versatile material, but its performance depends heavily on the specific grade and heat treatment process used.
What Types of Martensitic Stainless Steel Grades?
Each grade is designed to balance hardness, corrosion resistance, and machinability, allowing manufacturers to choose the best fit for their needs:
- 410: A basic martensitic grade with about 11.5-13.5% chromium and low carbon content. It offers good corrosion resistance and moderate strength, often used in cutlery and valve components.
- 420: Higher carbon content than 410, making it harder and more wear-resistant. Commonly used for surgical instruments, knives, and scissors.
- 440 Series (440A, 440B, 440C): These grades have increasing carbon content, with 440C being the hardest and most corrosion-resistant of the group. They’re popular for high-quality knife blades and bearings.
- 17-4 PH: A precipitation-hardening martensitic stainless steel with added nickel and copper. It offers excellent strength and corrosion resistance, used in aerospace and chemical processing.
- 416: Contains added sulfur for improved machinability, making it easier to work with in manufacturing processes. Often used for screws, bolts, and gears.
What Are the Applications of Martensitic Stainless Steel?

From everyday items like kitchen knives to high-tech aerospace components, martensitic stainless steel is a workhorse material across industries:
- Cutlery and Blades: Grades like 420 and 440C are widely used for knives, scissors, and other cutting tools due to their hardness and ability to hold a sharp edge.
- Surgical Instruments: The combination of corrosion resistance and strength makes martensitic stainless steel ideal for medical tools like scalpels and forceps.
- Aerospace Components: Grades like 17-4 PH are used in aircraft parts, such as turbine blades, due to their high strength and resistance to fatigue.
- Mechanical Parts: Gears, shafts, and valves often use martensitic stainless steel for its wear resistance and durability in demanding environments.
- Firearms: The material’s toughness and corrosion resistance make it suitable for gun barrels and other firearm components.
- Industrial Tools: Dies, molds, and other tooling benefit from the steel’s ability to withstand heavy wear and tear.
What Are the Benefits of Martensitic Stainless Steel?
Martensitic stainless steel offers several advantages that make it a popular choice in machining and manufacturing:
- Exceptional Strength: Its ability to be heat-treated to high hardness levels makes it ideal for applications requiring durability.
- Versatility: With various grades available, manufacturers can select the perfect balance of hardness, corrosion resistance, and machinability.
- Cost-Effective: Compared to austenitic stainless steels, martensitic grades are often more affordable, offering a good balance of performance and cost.
- Magnetic Properties: Its magnetism is useful in applications like electric motors or magnetic clamps.
- Wear Resistance: The material’s hardness ensures long-lasting performance in abrasive environments.
What Are the Limitations of Martensitic Stainless Steel?
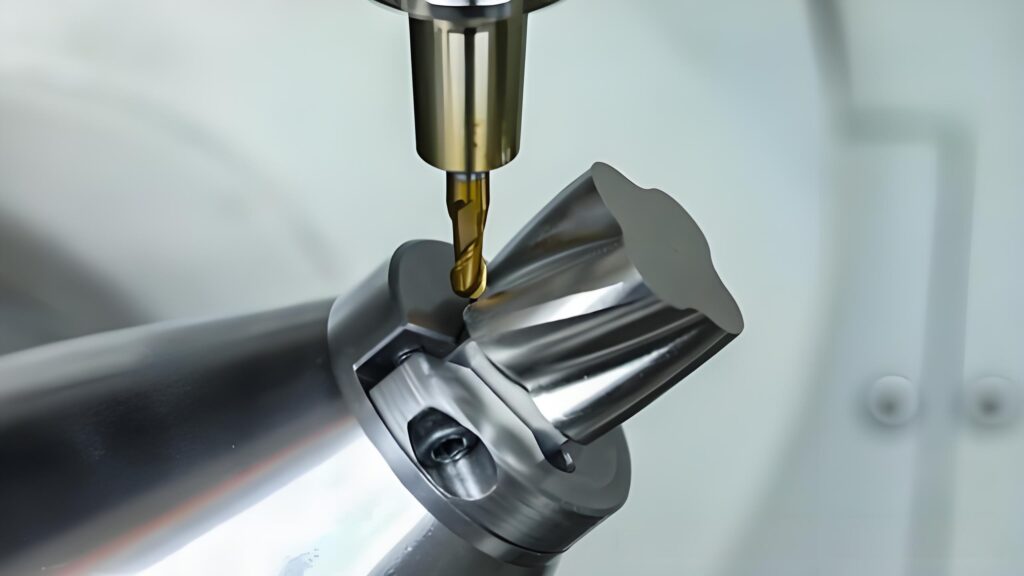
While martensitic stainless steel has many strengths, it also has some limitations that manufacturers need to consider:
- Lower Corrosion Resistance: Compared to austenitic or ferritic stainless steels, martensitic grades are less resistant to rust, especially in harsh environments like saltwater.
- Brittleness: High carbon content can make the material brittle, especially if not properly tempered, leading to potential cracking under stress.
- Challenging Machinability: The hardness that makes martensitic stainless steel durable can also make it difficult to machine, requiring specialized tools and expertise.
- Limited Weldability: Welding can be tricky due to the risk of cracking, often requiring preheating and post-weld heat treatment.
- Cost of Processing: The need for precise heat treatment and specialized machining can increase production costs.
Understanding these limitations helps manufacturers choose the right material and processing techniques to maximize performance.
How Does Martensitic Stainless Steel Compare to Other Stainless Steels?
- Austenitic Stainless Steel: Known for excellent corrosion resistance and formability, austenitic grades (like 304 and 316) are non-magnetic and softer than martensitic grades. They’re ideal for food processing and chemical environments but lack the hardness of martensitic steel.
- Ferritic Stainless Steel: Ferritic grades (like 430) are magnetic and offer good corrosion resistance but lower strength than martensitic steel. They’re often used in automotive exhausts and decorative applications.
- Duplex Stainless Steel: Combining austenitic and ferritic properties, duplex stainless steel offers high strength and corrosion resistance but is more expensive and complex to process.
Martensitic stainless steel shines in applications requiring hardness and strength, but its moderate corrosion resistance makes it less suitable for highly corrosive environments.
Heat Treatment
Heat treatment is what sets martensitic stainless steel apart. The process involves:
- Heating: The steel is heated to a high temperature (typically 980-1050°C) to transform its structure.
- Quenching: Rapid cooling “freezes” the martensitic structure, increasing hardness.
- Tempering: A secondary heat treatment reduces brittleness while maintaining strength.
This process allows manufacturers to tailor the material’s properties, balancing hardness with toughness. However, improper heat treatment can lead to issues like cracking or reduced corrosion resistance, so precision is critical.
Choosing the Right Grade for Your Project
Selecting the right martensitic stainless steel grade depends on the application. For example, if you’re making a high-quality knife, 440C might be the best choice for its hardness and edge retention. For a valve exposed to mild corrosion, 410 could be sufficient. Consulting with material experts and machinists ensures you pick the grade that meets your project’s needs.
Working with Martensitic Stainless Steel in Machining
Machining martensitic stainless steel requires care due to its hardness. Here are some tips for success:
- Use High-Quality Tools: Carbide or ceramic tools are often necessary to handle the material’s toughness.
- Optimize Cutting Parameters: Lower cutting speeds and higher feed rates can improve efficiency and tool life.
- Consider Heat Treatment Timing: Machining is often easier before full hardening, so plan your process accordingly.
- Coolant Use: Proper cooling prevents overheating and extends tool life.
Skilled machinists, like those at Precionn, can navigate these challenges to produce high-quality components.
The Future of Martensitic Stainless Steel
As industries evolve, martensitic stainless steel continues to find new applications. Advances in heat treatment and alloy design are improving its corrosion resistance and machinability, making it even more versatile. From sustainable manufacturing to cutting-edge aerospace designs, this material is poised to remain a staple in precision engineering.
Why Choose Precionn for Your Martensitic Stainless Steel Needs?
When it comes to working with martensitic stainless steel, partnering with an experienced machining company is essential. Precionn, a leader in the machining industry, specializes in crafting high-quality components from materials like martensitic stainless steel. With a commitment to precision and innovation, Precionn ensures that every project meets the highest standards of quality and performance. Whether you need custom parts for aerospace, medical, or industrial applications, Precionn’s expertise and state-of-the-art technology deliver reliable results. Visit our website to learn how we can bring your vision to life with martensitic stainless steel and other advanced materials.