Stainless steel is a cornerstone of the machining industry, prized for its exceptional corrosion resistance, durability, and aesthetic appeal. Its ability to withstand harsh environments while maintaining structural integrity makes it a preferred material for a wide range of applications, from kitchen equipment to marine hardware. Among the numerous stainless steel grades, 304 and 316 stand out as the most widely used due to their versatility and performance. At Precionn, a company specializing in precision machining, selecting the right stainless steel grade is critical to delivering high-quality components. This blog post provides an in-depth comparison of 304 vs 316 stainless steel, addressing their properties, applications, and differences, while also exploring how they compare to other grades like 430, 303, and 409. By understanding these distinctions, you can make informed decisions for your machining projects.
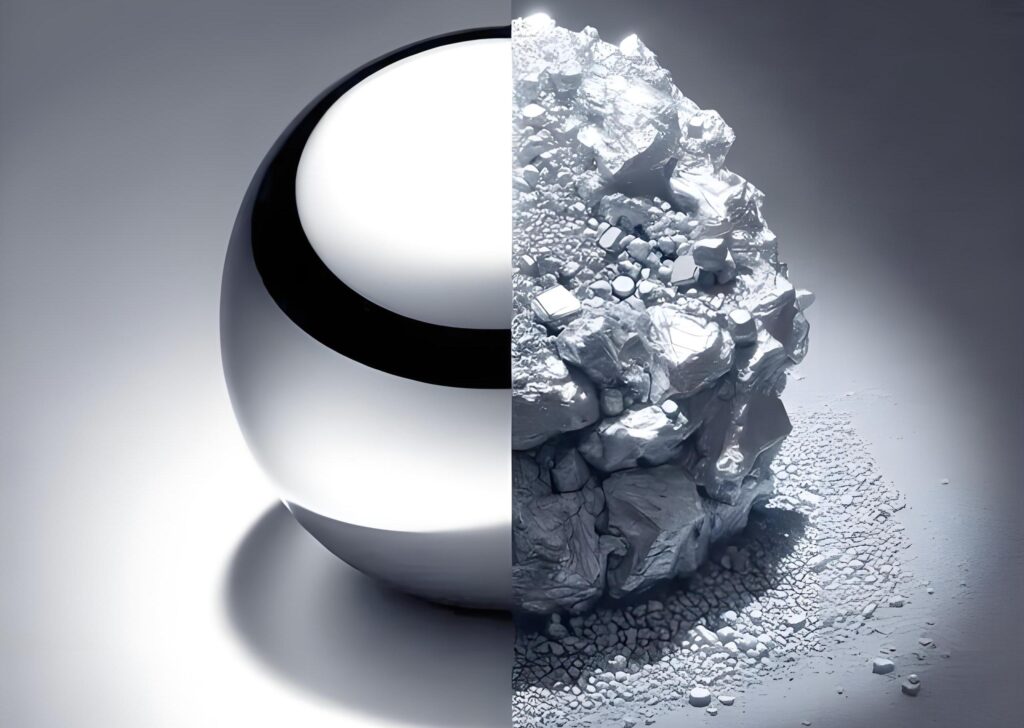
What is 304 Stainless Steel?
304 stainless steel, often referred to as “18/8” stainless steel, is an austenitic grade composed of 18-20% chromium and 8-10.5% nickel, with a maximum carbon content of 0.08%. This composition provides excellent corrosion resistance, making it suitable for a variety of environments. Its versatility stems from its formability, weldability, and ability to maintain a polished appearance, which is why it’s the most commonly used stainless steel grade globally.
304 stainless steel is highly resistant to corrosion from most oxidizing acids and general environments, though it can be susceptible to pitting in chloride-rich settings. It performs well at temperatures up to 870°C (1600°F) for intermittent use and 925°C (1697°F) for continuous use, making it suitable for high-heat applications. Its non-magnetic nature in the annealed condition and excellent formability make it a favorite for applications such as:
- Food Processing: Fryers, prep tables, and cookware, as it meets FDA sanitary regulations.
- Kitchen Equipment: Sinks, appliances, and silverware for hygiene and durability.
- Architecture: Siding, elevators, and bathroom stalls for aesthetic appeal.
- Medical Devices: Trays and surgical tools due to its non-reactive properties.
Additionally, 304 stainless steel is available in various surface finishes, from matte to mirror-like, allowing for customization in design-focused applications. Its ease of machining, compared to other grades, also makes it a cost-effective choice for many projects.
What is 316 Stainless Steel?
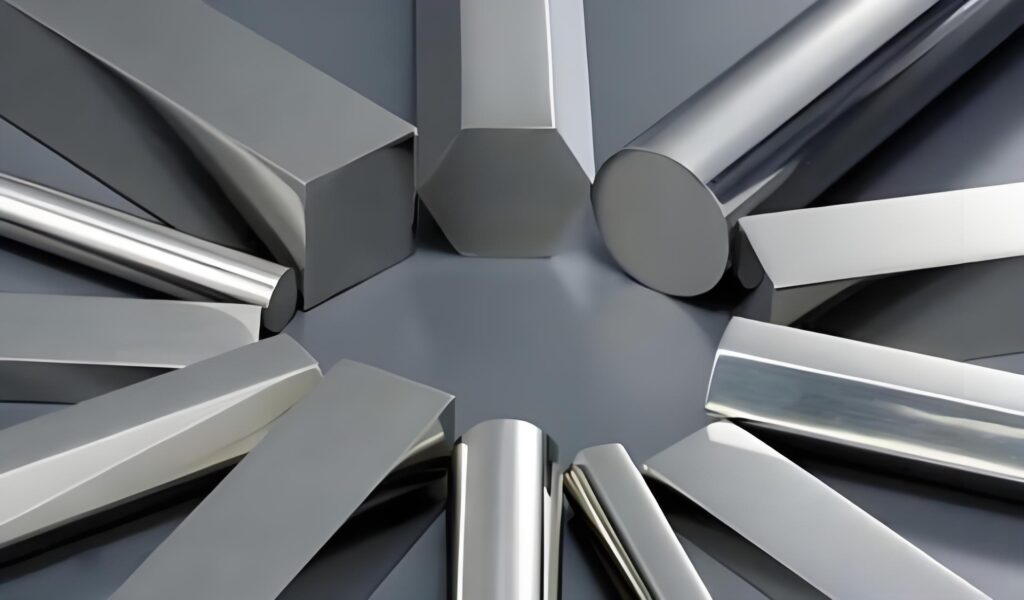
316 stainless steel is another austenitic grade, similar to 304 but with a key difference: the addition of 2-3% molybdenum. Its composition includes 16-18% chromium, 10-14% nickel, and a maximum carbon content of 0.08%. The molybdenum significantly enhances its corrosion resistance, particularly against chlorides, such as those found in seawater or de-icing salts, making it ideal for harsh environments.
This grade is often referred to as “marine-grade” stainless steel due to its superior performance in saline conditions. Like 304, it is non-magnetic in the annealed state, weldable, and formable, though its higher work hardening rate can make machining slightly more challenging. 316 stainless steel is commonly used in:
- Marine Applications: Boat rails, wire ropes, and ladders for saltwater resistance.
- Chemical Processing: Boilers, heaters, and storage tanks for chemical resistance.
- Pharmaceutical Equipment: Equipment requiring high cleanliness and corrosion resistance.
- Medical Devices: Surgical implants and tools for biocompatibility.
316 stainless steel also maintains good mechanical properties at elevated temperatures, performing best above 843°C (1550°F) and below 454°C (850°F). Its ability to resist pitting and crevice corrosion makes it a top choice for demanding applications where durability is paramount.
What is the difference between 304 and 316 stainless steel?
To understand what sets 304 and 316 stainless steel apart, it’s essential to examine their chemical compositions, mechanical properties, corrosion resistance, cost, and machinability. Below is a detailed comparison.
Chemical Composition
The primary distinction between 304 and 316 stainless steel lies in their alloy content, particularly the presence of molybdenum in 316.
Element | 304 (%) | 316 (%) |
Chromium | 18-20 | 16-18 |
Nickel | 8-10.5 | 10-14 |
Molybdenum | 0 | 2-3 |
The addition of molybdenum in 316 is the key factor enhancing its corrosion resistance, while the higher nickel content improves its toughness and ductility.
Performance Comparison
According to ASTM A240 standards, 304 and 316 stainless steel have similar mechanical properties, ensuring they are both robust for machining applications.
Property | 304 Stainless Steel | 316 Stainless Steel |
Tensile Strength (min) | 75 ksi (517 MPa) | 75 ksi (517 MPa) |
Yield Strength (min) | 30 ksi (207 MPa) | 30 ksi (207 MPa) |
Elongation (min) | 40% | 40% |
Hardness (max) | 201 HB | 217 HB |
While some sources suggest slight variations in tensile strength (e.g., 304 at 500-700 MPa vs. 316 at 400-620 MPa), standard specifications indicate comparable strength, making the choice more about corrosion resistance than mechanical performance.
Corrosion Resistance
Both grades offer excellent corrosion resistance, but 316 outperforms 304 in environments with high chloride exposure, such as coastal areas or chemical processing plants. The molybdenum in 316 provides superior resistance to pitting and crevice corrosion, making it ideal for marine and industrial applications. For example, structures like the Chicago Bean (Cloud Gate) are made from 316 stainless steel to withstand urban and environmental exposure. In contrast, 304 is sufficient for indoor or less aggressive environments, such as food processing or architectural applications.
Cost
316 stainless steel is typically 20-40% more expensive than 304 due to its molybdenum and higher nickel content. This cost difference can be significant in large-scale projects, making 304 a more economical choice when corrosion resistance requirements are moderate.
Machinability
In machining, 304 stainless steel is generally easier to work with than 316. The higher nickel and molybdenum content in 316 increases its work hardening rate, which can lead to greater tool wear and higher machining costs. However, with proper tooling and techniques, both grades can be machined effectively. For high-precision machining, 304 may be preferred to reduce production costs, as noted in resources like Geospace Technologies.
Heat Resistance
Both grades perform well at high temperatures, with 304 suitable for continuous use up to 925°C (1697°F) and 316 performing best above 843°C (1550°F) and below 454°C (850°F). However, prolonged exposure to high temperatures (425-860°C) may cause corrosion in 304, while 316 maintains better stability due to its molybdenum content.
Comparing 304 to Other Stainless Steel Grades
While 304 and 316 are the most common austenitic grades, other stainless steel grades like 430, 303, and 409 are used in specific applications. Below is a comparison to highlight their differences.
304 vs 430 Stainless Steel
430 stainless steel is a ferritic grade with 17% chromium and no nickel, making it magnetic and less corrosion-resistant than 304. It’s often used in cost-sensitive applications like automotive trim, appliance components, and architectural panels, where moderate corrosion resistance is sufficient. However, 430 is less resistant to acidic environments and may not perform as well as 304 in demanding conditions. Its lower cost makes it attractive for projects where budget is a priority, but 304 is preferred for superior corrosion resistance and formability.
304 vs 303 Stainless Steel
303 stainless steel is an austenitic grade similar to 304 but with added sulfur (0.15%) to enhance machinability. This makes it ideal for applications requiring extensive machining, such as nuts, bolts, and gears. However, the sulfur slightly reduces its corrosion resistance and weldability compared to 304. For projects prioritizing ease of machining over maximum corrosion resistance, 303 is a better choice, but 304 remains the standard for general-purpose applications.
304 vs 409 Stainless Steel
409 stainless steel is a ferritic grade with 11% chromium, designed for high-temperature applications like automotive exhaust systems. It offers moderate corrosion resistance and good heat resistance but is less durable in corrosive environments than 304. Its lower cost makes it suitable for applications where high temperatures are a concern, but 304 is preferred for better corrosion resistance and formability in general use.
Which is Better: 304 or 316 Stainless Steel?
The question of which is better—304 or 316 stainless steel—depends on the specific requirements of your project. If your application involves exposure to harsh environments, such as saltwater or aggressive chemicals, 316 stainless steel is likely the better choice due to its superior corrosion resistance. For example, marine hardware like boat rails or chemical processing equipment benefits from 316’s ability to resist chloride-induced corrosion. Conversely, for applications where corrosion is less of a concern, such as indoor kitchen equipment or architectural panels, 304 stainless steel offers excellent performance at a lower cost.
Consider a food processing plant: 304 stainless steel is often sufficient for sinks and countertops, as it resists corrosion from food acids and cleaning agents while meeting FDA standards. In contrast, a pharmaceutical facility handling aggressive chemicals might opt for 316 to ensure equipment longevity. Budget constraints also play a role, as 304’s lower cost can make it more appealing for large-scale projects with moderate corrosion requirements.
Which is Stronger: 304 or 316 Stainless Steel?
When comparing strength, 304 and 316 stainless steel are nearly identical according to ASTM A240 standards, with both having a minimum tensile strength of 75 ksi and yield strength of 30 ksi. Some sources suggest 316 may perform slightly better at elevated temperatures due to its molybdenum content, while others indicate 304 may have a slight edge in typical conditions. However, these differences are minimal, and strength is rarely the deciding factor. Instead, focus on corrosion resistance, cost, and machinability when choosing between them.
Practical Considerations for Machining
In the machining industry, the choice between 304 and 316 stainless steel can impact production efficiency and costs. 304 stainless steel is generally easier to machine due to its lower work hardening rate, which reduces tool wear and machining time. 316, with its higher nickel and molybdenum content, tends to work harden more quickly, potentially increasing tool wear and requiring more robust machining strategies. For high-precision components, machinists may prefer 304 to minimize costs, but 316 is often necessary for parts exposed to harsh environments.
Surface finishes also play a role in machining. Both grades can be finished to achieve a range of appearances, from brushed to polished, which is important for aesthetic applications like architectural panels. Additionally, both 304 and 316 are non-magnetic in the annealed state, but cold working can induce slight magnetism, particularly in 304, which may be a consideration for specific applications.
Real-World Applications
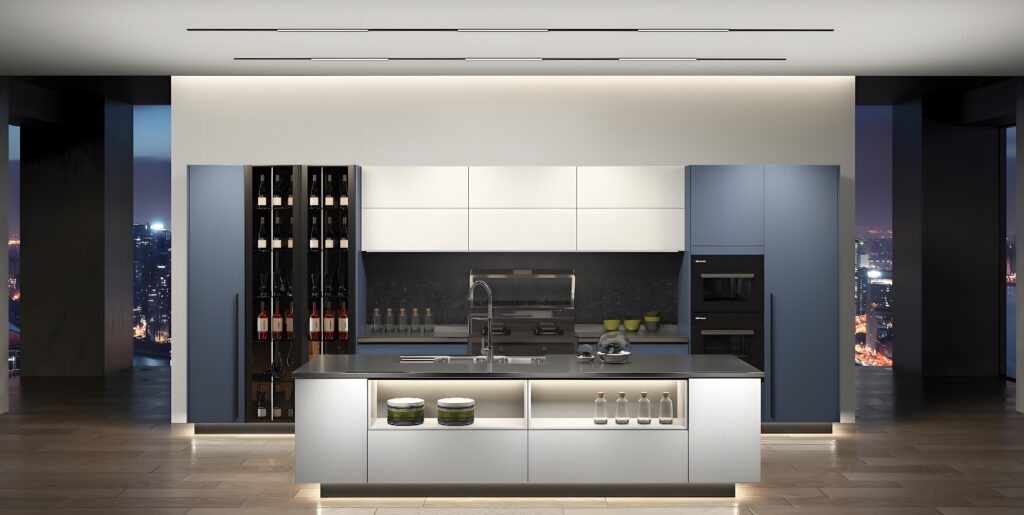
To illustrate the practical differences, consider the following examples:
- Food Industry: A commercial kitchen might use 304 stainless steel for sinks and countertops due to its corrosion resistance to food acids and cost-effectiveness. However, a coastal restaurant might choose 316 for outdoor fixtures to withstand salty air.
- Marine Applications: Boat fittings, such as railings and ladders, are typically made from 316 stainless steel to resist corrosion from seawater, whereas 304 might suffice for inland applications.
- Chemical Processing: Equipment like storage tanks or pipelines in chemical plants often uses 316 to handle aggressive chemicals, while 304 could be used for less corrosive substances.
These examples highlight the importance of matching the material to the environment and application requirements.
Conclusion
Choosing the right stainless steel grade is essential for ensuring the performance and longevity of machined components. 304 and 316 stainless steel each offer unique advantages, with 304 being a cost-effective, versatile option for general use and 316 excelling in corrosive environments. Other grades like 430, 303, and 409 serve specific purposes, from cost-sensitive applications to high-machining or high-temperature needs. At Precionn, we specialize in precision machining and have extensive experience working with various stainless steel grades. Our state-of-the-art facilities and skilled team can help you select the ideal material and deliver high-quality components tailored to your specifications. Contact Precionn today to discuss your project and discover how we can bring your designs to life.