When it comes to selecting the right metal for industrial, construction, or manufacturing purposes, the choice often narrows down to galvanized steel and stainless steel. These two materials are prevalent across a wide range of industries due to their durability, resistance to corrosion, and mechanical versatility. However, each has its own strengths, limitations, and ideal use cases.
At Precionn, a leading company specializing in precision machining solutions, understanding the properties and appropriate applications of metals is crucial to delivering high-quality outcomes. In this comprehensive guide, we delve into the fundamental differences and similarities between galvanized steel and stainless steel to help businesses, engineers, and manufacturers make informed decisions.
What is Galvanized Steel?
Galvanized steel is carbon steel coated with a layer of zinc through a process called galvanization, typically via hot-dip galvanizing or electro-galvanizing. The zinc acts as a protective barrier, shielding the underlying steel from corrosion and extending its lifespan in environments exposed to moisture or weathering. The core material is standard carbon steel, composed primarily of iron with small amounts of carbon and other elements. Galvanized steel is widely valued for its affordability and corrosion resistance, making it a popular choice for outdoor and industrial applications.
What is Stainless Steel?
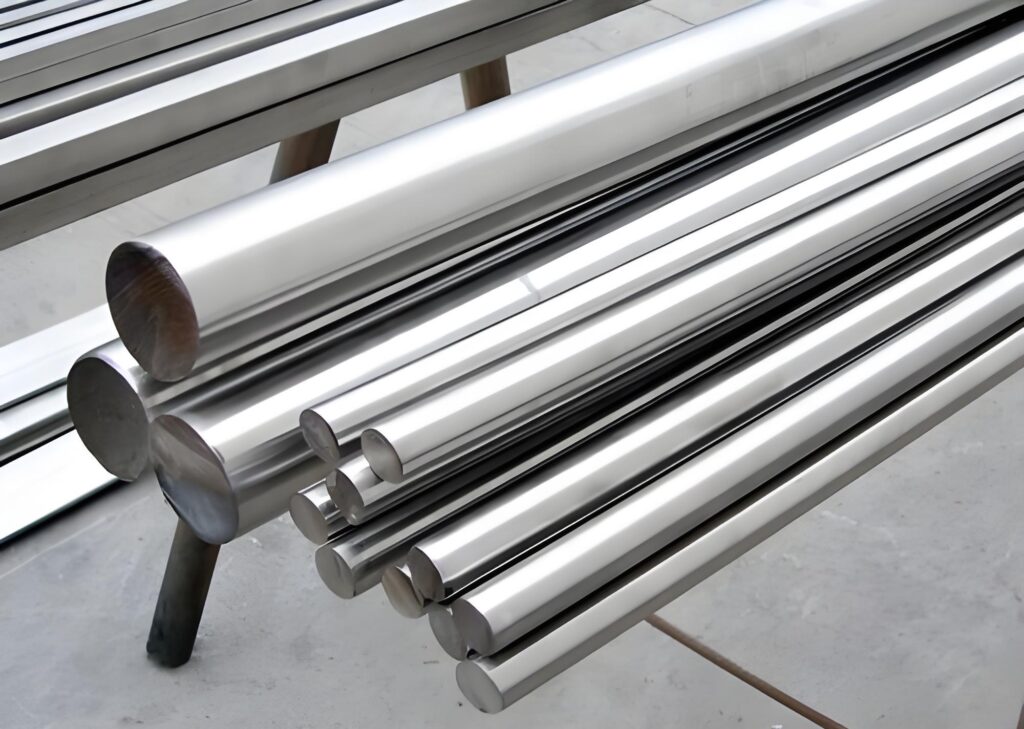
Stainless steel is an iron-based alloy containing at least 10.5% chromium, which forms a passive chromium oxide layer that protects the material from corrosion and staining. Additional elements like nickel, molybdenum, or titanium are often included to enhance specific properties, such as strength or resistance to extreme environments. Available in various grades (e.g., 304, 316, 430), stainless steel is prized for its durability, aesthetic appeal, and versatility, making it a preferred material in industries ranging from food processing to architecture.
Chemical Properties of Galvanized Steel vs. Stainless Steel
The chemical composition of a metal determines how it behaves in different environments, making it a critical factor in material selection. Let’s explore the chemical differences between galvanized and stainless steel.
Composition
Galvanized steel consists of a carbon steel core coated with zinc. The steel itself is primarily iron with trace amounts of carbon and other elements, while the zinc coating provides sacrificial protection, corroding before the steel does. The thickness of the zinc layer varies depending on the galvanization process, affecting its corrosion resistance.
Stainless steel is an alloy of iron, chromium, and often other elements like nickel or molybdenum. The chromium content creates a self-healing oxide layer, while additional alloying elements enhance specific properties. For example, 316 stainless steel includes molybdenum for superior resistance to pitting in harsh environments, such as marine settings.
Corrosion Resistance
Corrosion resistance is a key differentiator in the galvanized steel vs. stainless steel debate. Galvanized steel’s zinc coating offers excellent protection against rust, particularly in outdoor or humid conditions. However, if the zinc layer is scratched or worn away, the underlying steel becomes susceptible to corrosion, requiring maintenance or repair.
Stainless steel’s chromium oxide layer provides superior corrosion resistance, regenerating even after surface damage. This makes it highly effective in aggressive environments, such as coastal areas or chemical plants. Grades like 316 are particularly resistant to pitting and crevice corrosion, outperforming galvanized steel in long-term exposure to moisture or chemicals.
Reactivity to Chemicals
Galvanized steel can react to certain chemicals, especially acids or alkalis, which may erode the zinc coating over time. This limits its suitability for environments with frequent chemical exposure, such as industrial facilities handling corrosive substances.
Stainless steel is far less reactive, particularly in higher grades. Its resistance to acids, alkalis, and salts makes it ideal for industries like food processing, pharmaceuticals, and chemical manufacturing, where hygiene and chemical stability are critical.
Mechanical Properties of galvanized vs stainless steel
Mechanical properties influence a metal’s suitability for machining, structural integrity, and performance under stress. Here’s how galvanized and stainless steel compare.
Durability
Galvanized steel is durable in environments where corrosion is a concern, thanks to its zinc coating. However, its durability depends on the zinc layer’s thickness and the conditions it faces. Abrasive or high-impact environments can compromise the coating, reducing its lifespan.
Stainless steel is renowned for its exceptional durability, resisting both corrosion and physical wear. Its strength and toughness make it ideal for applications requiring long-term reliability, such as structural components or machinery subjected to heavy use. For high-stress projects, stainless steel often offers superior longevity.
Thermal Conductivity
Thermal conductivity is important for applications involving heat transfer. Galvanized steel, being primarily carbon steel, has moderate thermal conductivity, making it suitable for systems like HVAC or heat exchangers. The zinc coating slightly reduces its efficiency compared to uncoated steel.
Stainless steel has lower thermal conductivity due to its alloyed composition, which can be advantageous in applications requiring heat retention, such as cookware or industrial ovens. However, it’s less efficient for heat transfer, which may influence material choice in specific machining projects.
Melting Point
The melting point affects a material’s performance in high-temperature environments. Galvanized steel’s carbon steel core has a melting point of approximately 2,500–2,700°F (1,370–1,482°C). However, the zinc coating melts at around 787°F (420°C), limiting its use in high-heat applications.
Stainless steel’s melting point ranges from 2,550–2,790°F (1,400–1,532°C), depending on the grade. This higher melting point makes it more suitable for applications like furnace components, exhaust systems, or other high-temperature environments.
Weldability
Weldability is a critical consideration for machining projects. Galvanized steel can be welded, but the zinc coating presents challenges. Welding releases zinc fumes, which are hazardous and require proper ventilation. The coating may also cause weld imperfections, necessitating surface preparation.
Stainless steel is generally easier to weld, particularly with appropriate techniques and equipment. Grades like 304 are highly weldable, though higher grades like 316 may require specialized fillers to prevent cracking. For precision machining, stainless steel often provides greater welding flexibility.
Magnetism
Magnetism can impact certain machining processes or applications. Galvanized steel, being carbon steel at its core, is typically magnetic, which can be beneficial for processes like magnetic clamping or sorting.
Stainless steel’s magnetism varies by grade. Austenitic grades (e.g., 304, 316) are generally non-magnetic, while ferritic and martensitic grades (e.g., 430) are magnetic. This distinction is crucial for industries like electronics or medical device manufacturing, where non-magnetic materials may be required.
Other Comparisons of Galvanized Steel vs. Stainless Steel
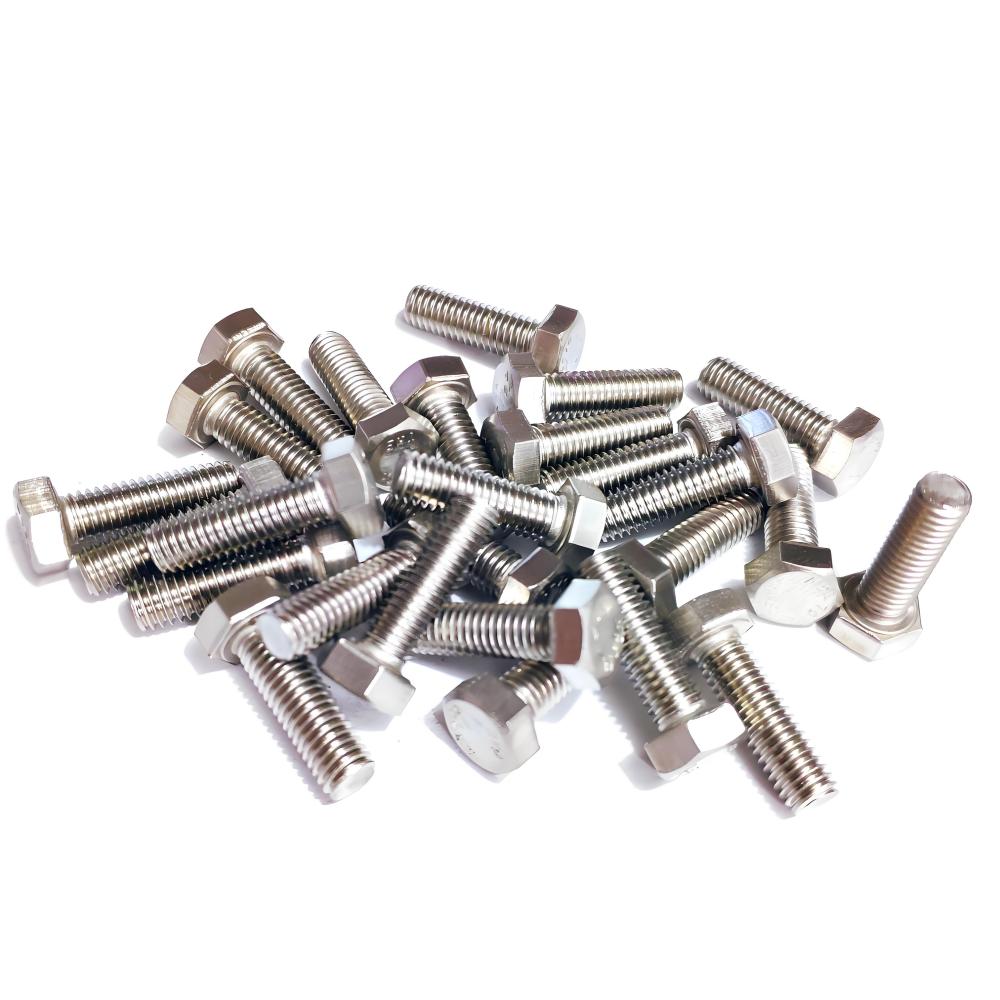
Beyond chemical and mechanical properties, additional factors influence material selection. Let’s examine these considerations.
Cost
Cost is often a primary concern in material selection. Galvanized steel is generally more affordable than stainless steel, making it a go-to choice for large-scale projects like construction or infrastructure. The galvanization process is cost-effective, providing corrosion resistance at a lower price point.
Stainless steel, due to its alloyed composition and superior properties, commands a higher price. However, its longevity and low maintenance needs can offset the initial cost in applications where durability is paramount. For budget-conscious projects, galvanized steel is often preferred, while stainless steel suits premium applications.
Appearance
Aesthetics play a role in applications where visual appeal matters. Galvanized steel has a shiny, spangled finish from its zinc coating, which can dull over time as the zinc weathers. It’s typically chosen for functional rather than decorative purposes.
Stainless steel offers a sleek, polished appearance that maintains its luster over time. Available in finishes like brushed or mirror, it’s a favorite for architectural features, automotive components, and consumer goods where aesthetics are a priority. For projects requiring a high-end look, stainless steel is the clear choice.
Weight
Weight impacts transportation, installation, and structural design. Galvanized steel is slightly heavier due to its zinc coating, though the difference is minimal compared to uncoated carbon steel. It’s suitable for heavy-duty applications like structural frameworks.
Stainless steel’s weight varies by grade but is generally comparable to galvanized steel. Its superior strength-to-weight ratio allows for thinner, lighter components in certain designs, which can be advantageous in machining projects where weight is a concern.
Maintenance
Maintenance requirements affect long-term costs and performance. Galvanized steel requires minimal maintenance in mild environments, but damage to the zinc coating may necessitate repairs or recoating. Regular inspections can help prolong its lifespan.
Stainless steel is low-maintenance, resisting corrosion and staining without additional coatings. Simple cleaning with mild detergents keeps it pristine, making it ideal for applications like medical equipment or kitchen appliances where upkeep must be minimal.
Environmental Impact
Sustainability is increasingly important in material selection. Galvanized steel is recyclable, but the galvanization process involves energy-intensive steps and chemicals, which can have environmental implications. Zinc leaching into soil or water is also a potential concern.
Stainless steel is highly recyclable, often containing a significant percentage of recycled material. Its long lifespan reduces the need for replacements, making it an eco-friendly choice for sustainable projects. For environmentally conscious industries, stainless steel aligns better with green initiatives.
Applications of Galvanized Steel vs. Stainless Steel
The choice between galvanized and stainless steel often hinges on the intended application. Galvanized steel is widely used in construction (e.g., roofing, fencing, structural beams), automotive parts, and agricultural equipment. Its affordability and corrosion resistance make it ideal for outdoor structures exposed to weather.
Stainless steel excels in industries requiring hygiene, durability, or aesthetics. Common applications include food processing equipment, medical instruments, marine hardware, and architectural features like railings and facades. Its versatility makes it a top choice for precision machining in demanding environments.
Commonalities of Galvanized Steel and Stainless Steel
Despite their differences, galvanized and stainless steel share several characteristics. Both are iron-based, offering strength and versatility for machining. They provide corrosion resistance, albeit through different mechanisms (zinc coating vs. chromium oxide layer). Additionally, both are recyclable, supporting sustainable manufacturing practices. Recognizing these commonalities highlights their shared strengths while underscoring their unique advantages.
So Which Metal Is Best for Your Needs?
Choosing between galvanized steel and stainless steel depends on your project’s specific requirements, budget, and environment. Galvanized steel is a cost-effective, durable option for applications where corrosion resistance is needed but aesthetics are secondary, such as construction or industrial frameworks. Stainless steel, with its superior corrosion resistance, durability, and polished appearance, is ideal for high-end applications like medical devices, food processing, or architectural designs.
At Precionn, we understand the complexities of material selection in machining. Our expertise ensures that whether you choose galvanized or stainless steel, your components are crafted with precision and quality. Visit our website to discover how Precionn can deliver tailored machining solutions to meet your unique project needs.