Stainless steel is widely recognized for its durability, corrosion resistance, and sleek appearance. It’s used in everything from kitchen appliances and surgical instruments to aerospace and marine applications. But despite its reputation, a common question still lingers: does stainless steel rust?
At Precionn, a precision machining company specializing in high-performance components, customers often ask about the rust resistance of stainless steel. Understanding the truth behind stainless steel corrosion is crucial—not only for selecting the right materials but also for ensuring the long-term success of any engineering project.
In this blog, we’ll take a deep dive into how stainless steel behaves under different conditions, when it might rust, and how to prevent that from happening.
Will Stainless Steel Rust?
Despite the name “stainless,” stainless steel is not completely immune to rust. The term “stainless” refers to its enhanced resistance to corrosion compared to regular steel. However, under the right conditions, even stainless steel can corrode—especially if it’s not the appropriate grade for the environment.
What Makes Stainless Steel “Stainless”?
Stainless steel contains a minimum of 10.5% chromium, which reacts with oxygen to form a thin, invisible passive layer of chromium oxide on the surface. This layer protects the metal beneath from moisture, air, and corrosive substances.
However, if this passive layer is damaged or unable to reform, corrosion can begin. Factors like exposure to chlorides, high humidity, or poor maintenance can cause this breakdown.
why does stainless steel rust?
Understanding why and how stainless steel rusts involves considering a combination of environmental and mechanical factors.
1. Chloride Exposure
Chlorides, such as those found in saltwater, swimming pools, and even tap water in some regions, are particularly aggressive to stainless steel. Chloride ions can penetrate the passive layer and trigger pitting corrosion, especially on lower-grade stainless steels like 304.
2. Mechanical Damage
Scratches, machining marks, or physical damage to the surface of stainless steel can compromise the protective chromium oxide layer. If not properly maintained, these areas become entry points for corrosion.
3. High Temperatures and Humidity
High humidity or temperatures can accelerate corrosion, especially in enclosed or poorly ventilated spaces. These conditions can encourage crevice corrosion or intergranular corrosion, depending on the alloy.
4. Chemical Exposure
Acids, cleaning chemicals, and industrial solvents can also degrade the passive layer. This is particularly relevant in pharmaceutical, food processing, or manufacturing industries.
5. Improper Maintenance or Cleaning
Using chlorine-based cleaners, steel wool, or neglecting regular maintenance can result in surface contamination or scratching. Once contaminated, even high-grade stainless steel may begin to rust.
6. Contamination from Carbon Steel
In workshops or fabrication environments where carbon steel particles come into contact with stainless steel, rust can appear. This type of corrosion is not from the stainless steel itself, but from embedded carbon steel contaminants.
Types of Stainless Steel Corrosion

Not all corrosion is the same. Understanding the types of corrosion can help engineers and product designers choose the best materials and methods for prevention.
1. Pitting Corrosion
This occurs when small holes form on the surface due to chloride attack, especially in stagnant conditions. Pitting can be hard to detect but is dangerous because it can lead to structural failure.
- Common in: Marine environments, swimming pools
- Affected grades: 304, lower alloys
2. Crevice Corrosion
Happens in narrow gaps or areas where water or chemicals can get trapped and stay stagnant, such as under gaskets, washers, or deposits. Without oxygen, the passive layer can’t reform, and corrosion begins.
- Common in: Bolted connections, flanges
- Prevention: Use of appropriate design and sealing materials
3. Galvanic Corrosion
When stainless steel is in electrical contact with a more reactive metal (e.g., aluminum or carbon steel), the more reactive metal corrodes faster. In this electrochemical reaction, even stainless steel may show signs of damage.
- Prevention: Electrical insulation between dissimilar metals
4. Intergranular Corrosion
Occurs along the grain boundaries of stainless steel, typically caused by improper heat treatment or high-temperature exposure during welding.
- Prevention: Use of low-carbon grades like 304L or 316L
5. Stress Corrosion Cracking (SCC)
A combination of tensile stress and corrosive environment can lead to cracking. It’s a concern in industries with high-pressure systems or boilers.
- Common in: Petrochemical plants, power stations
- Affected grades: Certain austenitic steels under stress
Stainless Steel Rust Prevention
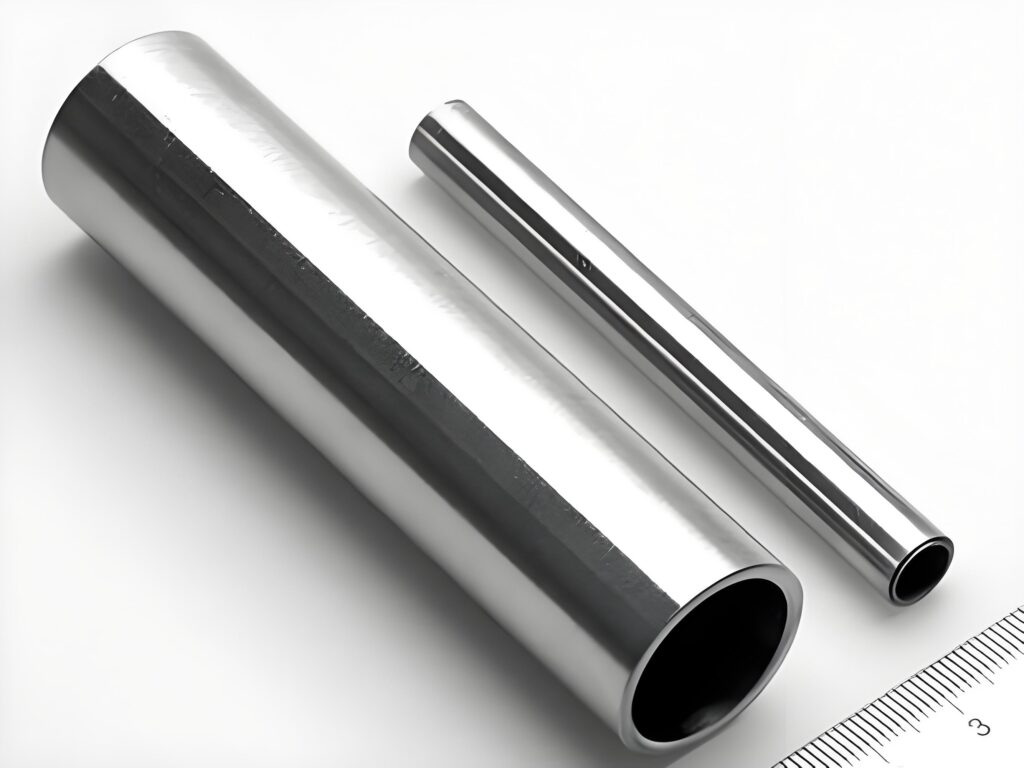
While stainless steel can rust under specific conditions, there are many strategies to prevent corrosion and maximize its lifespan.
1. Choosing the Right Grade
Selecting the correct alloy is the first step. Here are some commonly used stainless steels and their properties:
- 304 Stainless Steel: General-purpose, good corrosion resistance
- 316 Stainless Steel: Enhanced resistance to chlorides and marine environments
- 430 Stainless Steel: Ferritic grade with moderate corrosion resistance, often used in appliances
- Duplex Stainless Steel: Combines austenitic and ferritic structures; strong and corrosion-resistant
2. Proper Surface Finishing
Finishing techniques like electropolishing, passivation, and mechanical polishing help improve the passive layer and surface cleanliness.
- Passivation: Removes iron contaminants and strengthens the passive film
- Electropolishing: Smooths the surface to remove imperfections and reduce corrosion risk
3. Regular Cleaning and Maintenance
Cleaning stainless steel with non-chloride cleaners and using soft cloths helps prevent surface contamination. Avoid steel wool or abrasive pads.
4. Proper Design Considerations
Good design practices reduce corrosion risks:
- Avoid tight crevices or water-trapping geometries
- Ensure good drainage and ventilation
- Use non-metallic washers between dissimilar metals
5. Protective Coatings
In aggressive environments, stainless steel can be coated with protective layers, such as:
- Powder coatings
- Ceramic coatings
- Anti-corrosive paints
These act as an additional barrier against the elements.
6. Cathodic Protection
In large-scale applications, such as pipelines or ships, cathodic protection systems may be used to prevent electrochemical corrosion.
Common Applications and Corrosion Concerns
Marine Industry
Saltwater exposure can cause rapid pitting. Using 316 stainless steel or duplex grades is essential.
Food and Beverage Processing
Frequent cleaning and exposure to acidic or salty substances demand high-purity stainless steel, often with special surface treatments.
Medical and Pharmaceutical Equipment
Hygiene and chemical resistance are critical. Electropolished and passivated surfaces are standard.
Construction and Architecture
Structures exposed to rain, pollution, and varying temperatures must be carefully designed and maintained.
When Stainless Steel Rusts: What To Do?
If rust appears, it’s not the end of the road. Stainless steel can often be cleaned, restored, and re-passivated. Common restoration techniques include:
- Mechanical cleaning (fine abrasives, polishing)
- Chemical cleaning (citric acid or nitric acid passivation)
- Electrochemical restoration
After removing the rust, proper ongoing maintenance can prevent recurrence.
Common Myths About Stainless Steel Rust
There are several misconceptions about stainless steel and its corrosion resistance. Let’s debunk a few:
- Myth 1: Stainless Steel Never Rusts While stainless steel is highly resistant to rust, it’s not completely immune. Harsh environments or improper maintenance can lead to corrosion.
- Myth 2: All Stainless Steel Grades Are the Same Different grades offer varying levels of corrosion resistance. Choosing the right grade is critical for specific applications.
- Myth 3: Rust Means Poor Quality Rust on stainless steel is often due to external factors, such as contamination or environmental exposure, rather than the material’s quality.
Conclusion
So, does stainless steel rust? The answer is: yes, under certain conditions. However, with proper material selection, design, and maintenance, stainless steel remains one of the most corrosion-resistant and durable materials available today.
At Precionn, we understand the complexities of stainless steel machining, fabrication, and corrosion control. Whether you’re producing parts for aerospace, medical devices, or marine hardware, choosing the right material—and treating it correctly—makes all the difference.
Our team offers guidance on material selection, surface treatments, and post-machining care to ensure your components perform flawlessly in their intended environment. From prototype to production, we uphold the highest standards of quality and durability.
FAQ:
304 stainless steel is highly corrosion-resistant due to its chromium content (18-20%) but can rust under specific conditions, like prolonged exposure to chlorides (e.g., saltwater) or harsh environments without proper maintenance. Pitting or surface rust may occur in aggressive conditions.
316 stainless steel, with added molybdenum (2-3%), offers superior corrosion resistance compared to 304, especially in chloride-rich environments like saltwater. While it’s less likely to rust, it’s not immune and can still corrode under extreme conditions, such as prolonged exposure to high-salinity or acidic environments.
Stainless steel generally resists rust in fresh water due to its protective chromium oxide layer. However, prolonged submersion, especially in stagnant or contaminated water, can lead to localized corrosion (e.g., pitting) if the oxide layer is compromised.
Saltwater is more aggressive due to chlorides, which can break down the passive oxide layer. 304 stainless steel is more prone to rust in saltwater, while 316 is more resistant but not entirely immune. Regular cleaning and maintenance reduce the risk.
Stainless steel can resist rust outdoors, but exposure to harsh weather, pollutants, or coastal environments with salt-laden air can cause surface rust or pitting over time, especially for 304. 316 performs better in such conditions.
The time it takes for stainless steel to rust depends on the grade (e.g., 304 vs. 316), environmental factors (e.g., humidity, salinity, pH), and maintenance. In mild conditions, stainless steel may never rust. In aggressive environments like saltwater, 304 might show signs of corrosion within weeks to months if untreated, while 316 could take significantly longer. Regular cleaning can prevent rust indefinitely.